Containerization introduction
- Vegard Synnes
- Feb 26, 2019
- 5 min read
Updated: Apr 28, 2023
At Kar-Tainer we provide solutions to optimize containerization for CBU (completely built-up) vehicle and SKD (semi knocked-down) vehicle transportation. Having been operating in this niche since the early 1990’s, we consider ourselves somewhat of an authority within the field. Through a series of LinkedIn articles over the coming months, we aim to pass on some of the extensive knowledge we have built up to whoever is interested in learning more about the world of vehicle containerization.
We will be looking into specific areas where vehicle containerization is utilized, the technical aspects of loading cars in containers with racking systems, as well as the value creation enabled by containerization, for the different parties involved in the automotive supply chain.
To kick this all off we’ll do a close-up look at the two different focus areas of Kar-Tainer; containerization of CBU & SKD.
CBU Vehicle Containerization
Completely built-up vehicles are as the name suggests; finished built, self-propelled vehicles which are ready to be shipped from manufacturing or assembly plant to end-user. A significant portion of vehicles produced around the world will not be sold in its “Home marked”, but rather exported to a different country. For global transport of vehicles, ocean is by far the most popular transportation mode; according to Drewry Shipping Consultants the global seaborne vehicle trade volume was around 37.5 million CEU* (car equivalent units) in 2017. Out of which most vehicles are transported on specialized car-carriers.
An alternative to conventional RoRo transport is containerization. Loading vehicles in a container enables the shipper to tap into the multi-modal network built up around the container box, transporting by road, rail or ocean separately or in any combination required to get the cars from origin to destination.
When containerizing cars for outbound transportation, a couple key factors come in to play:
Safety of car and people; the equipment used and the stevedores loading the car need to be well design and properly trained. The vehicle needs to be properly secured inside the container in order to avoid shifting during transport and handling. As in all manual logistics operations it is important to reduce the chance of accident by limiting workers from entering the container or doing manual labor beneath the elevated vehicle.
Utilization of the container space; a standard 40-foot shipping container can only fit two vehicles when parked flat on the container floor, however this does far from fully utilize the total space of the container. Using a racking system can help increase the load factor to three-, four-, or even five-units per container.
Loading efficiency; efficient logistics comes down to how quick and precise a certain process can be carried out. If it takes half a day and a high head-count is required to load a container with vehicles, much of the potential cost saving is lost both on time spent and on labor cost. To ensure this does not happen, having the right method and equipment enabling efficient loading operations is important.
Cost optimization; cost control is always of high importance in logistics, also when shipping cars in containers. Having a system that can be used over again and again will cut costs substantially compared to using one-time or expandable loading systems. In the world where Green Logistics is becoming ever more important, returnable racking equipment can be of great value, helping shippers to become greener while at the same time saving money.
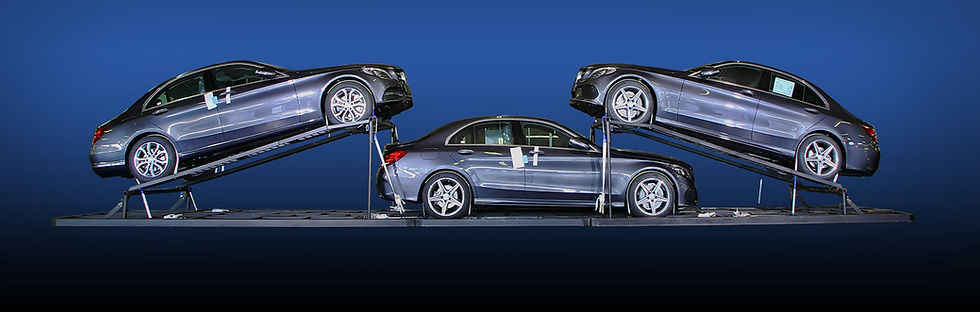
Kar-Tainer’s reusable CBU racking solutions have been tried and tested over the years to fulfill all criteria for providing safe, reliable and efficient containerization solutions of Completely Built-Up Vehicles. With our leasing model we enable auto-shippers to stay both lean and green.
SKD Vehicle Shipping
Semi knocked-down vehicles usually consist of a kit with a complete welded car body, coated and often pre-painted. SKD shipments can hold all parts required to assemble a full-functioning vehicle, or only key components such as the car body while smaller parts are localized in the market of assembly. SKD shipments is almost as old as the automotive industry itself as the Ford Motor Company was already shipping knocked-down components to its secluded domestic and overseas assembly plants as early as the 1920’s. Today, global automotive manufacturers utilize SKD shipments to benefit from lower import/sales taxes and to bolster local industry in countries where their cars are sold. Data from the UN Comtrade Database shows that more than 1.3 million car bodies were exported from top 8 exporting countries in 2017**. The biggest SKD exporting countries being USA, Germany, Slovakia, Czech Republic, Spain, Russia, Sweden and China.
When shipping SKD vehicles around the world, it is important to:
Optimize load factor; the more you pack into one container, the lower your shipping cost will be. Whether car bodies and associated parts are shipped in different or same container it is vital to utilize as much of the space in the container as possible. Seats, engine and transmission can be stored inside the body, while smaller parts can be packed up in boxes and stored in the vehicle trunk or in excess container space surrounding the car body.
Standardize packaging procedures; as anything else in the automotive supply chain, the packaging procedures for SKD vehicles need to follow a set of principles aimed at maximizing efficiency. Equipment which is easily assembled, facilitates efficient loading, and can be moved from loading- to storage-area and further into container, will increase output drastically.
Eliminate waste; one time use packaging material such as wood requires time and effort to both build up and break down. It also generates a lot of waste, both in the traditional sense of the word, and in the supply chain sense of the word. Filling up assembly facilities with wooden packaging creates a whole set of process and activities which could be eliminated with a re-usable system. In addition to this, wooden packaging is not cheap, and will add hundreds of dollars extra cost to each container shipped.

Kar-Tainer’s reusable SKD solution is based on the same module as our CBU system; it is easily assembled and enables simple handling both at loading facilities and during transport. It helps shippers cut waste and optimize their procedures for global SKD shipments.
Concluding Words
Whether we’re talking CBU or SKD shipments, the common denominator is the container, “The box that changed the world” as termed by Arthur Donovan and Joseph Bonney. This is also where we draw our inspiration; Kar-Tainer. Follow us in the coming months as we look closer on how the world of containerization of works; how to load CBU & SKD vehicles in containers, important container markets, and the opportunities up for grab for either shippers, carriers or 3PL’s involved in this sector.
* Drewry Shipping Consultants; Finished Vehicle Shipping Annual Review & Forecast ANNUAL REPORT 2018/19
** UN Comtrade Database reporting on HS870710 global export of Vehicles; bodies (including cabs) for the motor vehicles of heading no. 8703
Comments